Direct injection fuel rail Testing
Market Driver:
Gasoline Direct Injection (GDI) is a modern fuel injection technology employed in today’s gasoline engines. The gasoline is highly pressurized, and injected via a common rail fuel line directly into each cylinder, as opposed to conventional multi-point fuel injection that happens in the intake tract, or cylinder port. In most applications, gasoline direct injection creates lean burn combustion for improved fuel efficiency, and reduced emission levels. This new technology requires testing at lower leak rates not only to assure regulated emission standards are adhered too but also assure increased safety from leaks created from higher operational pressure.
Test Requirement:
Production demands (cycle time) and test specifications (low leak rates and test pressure) for GDI type products offer few test options that will provide the test performance (gage R&R) needed for product reliability in operation. Hard vacuum helium mass spectrometry is ideally suited for this application.
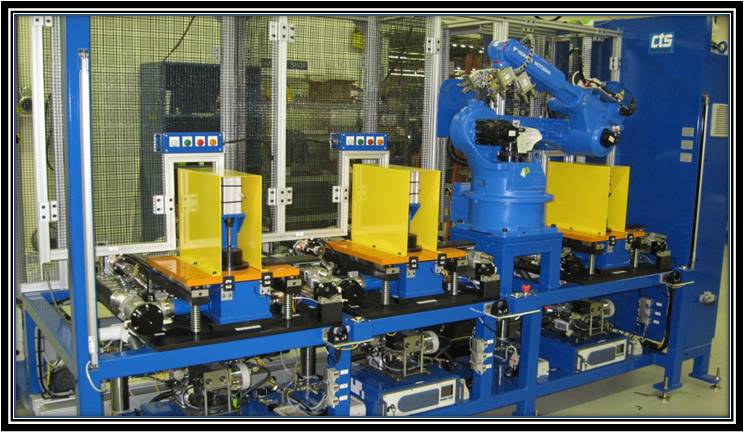
Challenges:
Any application involving high pressure testing, no matter what test technology is used, requires an expertise in sealing the part without marring or deforming the part or seal points. In addition, when using helium or other tracer gases, the integration process must also consider permeation of the tracer gas through the seals to avoid background concerns that may deteriorate test conditions. Lastly the reduction of human interface improves safety and assures proper processing of failed parts to keep them from getting back into the production process.
CTS Solution:
CTS engineers designed tooling that was flexible enough to accommodate positional tolerances of the injector and other ports to avoid distortion and any marring. We also developed seals that significantly reduce permeation of the tracer gas, can withstand higher temperatures, and are optimized to the right durometer or hardness, thus improving test performance and longevity. In the system shown above the automated robotic test cell conducts a hard vacuum helium mass spectrometer leak test on the fuel rails. Three independent hard vacuum chambers maintain the required production rate. The independent modular design minimizes down time for system maintenance. Tested parts are sorted pass/fail onto customers conveying system to assure the highest of quality in test and processing.
Cincinnati Test Systems has specialized in the design and build of multiple direct injection fuel rail test systems, all uniquely designed to meet the customer’s production environment. Contact us today for more information.